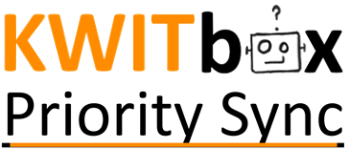
KWITbox Priority Sync adds to Zone Skipping by assigning a priority to all the open supply orders relative to inventory on hand. Using ASCM certified Demand Driven Execution Planning methods, Priority Sync:
• Creates a dynamic, priority gauge for each SKU/Location (SKUL) in your supply chain
• Monitors on hand inventory of your supply chain
• Assigns priorities to the orders replenishing these locations based upon urgency
• Support zone skipping based upon actual supply chain need
PRIORITY SYNC Functions
Incl.
The following 9 functions serve as a roadmap for how Synchronized Priority can be deployed to fit your company’s specific requirements. Rearranging or editing the functions to your supply chain ensures a ‘custom’ solution that all of the stakeholders of your supply chain can use and benefit.
Booking
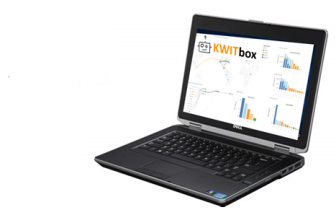
This function creates the unique serial number for each carton which you simply print locally, ideally at your vendor, as a label. The purchase order number, line/sku number and quantity open are all validated and directly assigned to each specific box. When the SKU is lot controlled, lot number and expiration date are also captured so that you Know What’s In The Box for Compliance.